Bär Cargolift - Lifting Performance. Since 1981.
Since the company was founded in 1981, BÄR has been committed to continuous enhancement. The focus is on the performance of its tail lifts in a wide range of transport tasks, where the Cargolift becomes an integral part of the overall commercial vehicle system. Immerse yourself in the history of this medium-sized, owner-managed family business. Discover the decades of expertise in the development and production of aluminium platforms as well as the innovative solutions that have often had and continue to have an influence on the industry. Because innovations can be copied - but innovative ability cannot. It is our basis for continuous enhancement at BÄR.
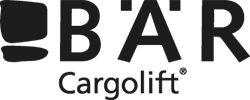
An era finally comes to an end (2025)
BÄR bid a silent farewell to its founder Gerd Bär in February. Gerd Bär laid the foundations for the successful company and its employees with his founding courage and tireless creativity. We will remember him as an energetic, straightforward and sincere person.
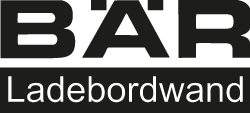
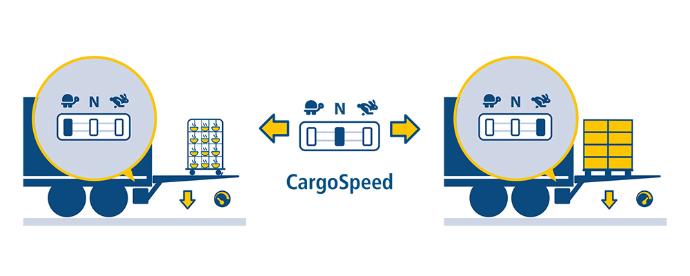
You decide how fast it goes! (2024)
Whether you want to deliver ready-to-serve soups in plates without spilling or unload pallets as quickly as possible - BÄR is working on speed control and infinitely variable speed regulation for all functions of its Cargolifts. Patent-protected and in continuous development.
BÄR brings light into the darkness! (2024)
When NightGuide becomes an indicator! At the IAA 2024, BÄR is presenting the flashing platform edge NightGuide as an approvable study for direction indicators (i.e. turn signals) and will make visitors' eyes light up!
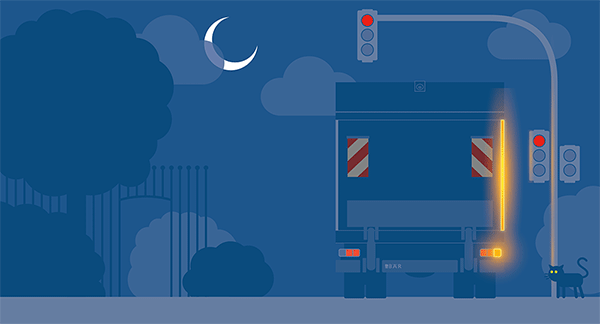
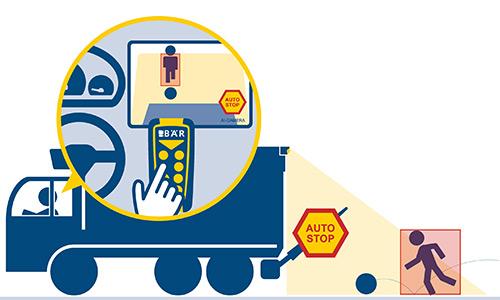
Safety first! Safety and digitalization (2023)
How about the platform stopping automatically if there is a risk of collision? The new VisionAssist assistance system uses AI rear-view cameras. If the camera detects a person within the platform's movement radius, the operating command immediately stops automatically - regardless of the control element used. The hazardous situation is directly displayed to the driver on the monitor in the cab. At the Bär Control EVO operating unit, the detected danger can be signaled with the red LED status display.
Certified sustainability at both production sites (2023)
Future viability is also a question of sustainability. That is why BÄR is carrying out energy audits at both production sites in 2022 and 2023 - with very good results. In addition, the hall roof of Gerd Bär GmbH in Heilbronn, Germany is equipped with a photovoltaic system in 2023. In strong sunlight, the medium-sized family business is thus achieving a peak output of up to 749 kW and save 500 t of CO2 per year!
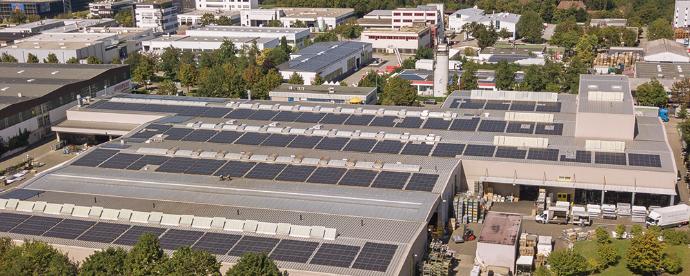
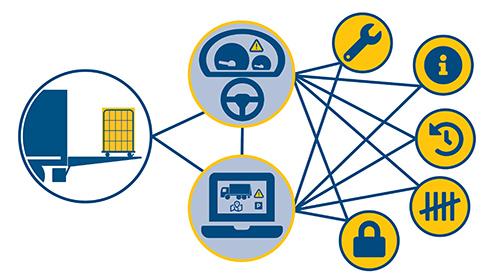
Data interface DIN 4630 (2021)
Tobias Bär also sees his Cargolift as an "integral part of the overall commercial vehicle system". His focus is on the digitalisation of the logistics chain. That is why he has been campaigning since 2017 in the VDA Standards Committee / DIN for a standardised data interface for the communication of body components with telematics and with the chassis/trailer. A cost-effective networking of all components will be possible. DIN 4630 will be adopted in 2021.
CO2-neutral production of welded steel assemblies (2021)
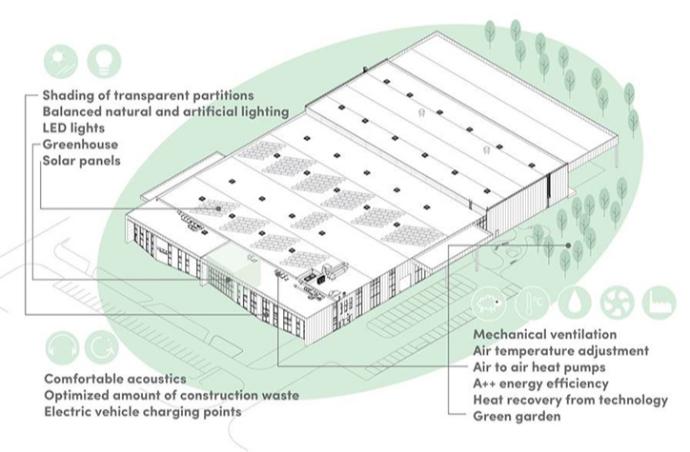
EasyFold automatic function for HydFalt (2021)
One operating command is enough and EasyFold automatically moves the Bär Cargolift HydFalt from the driving to the working position, including the platform folding. More operating comfort is not possible.
Bär Baltic Production (2021)
While the traditional site in Heilbronn, Germany, concentrates on the core competence of aluminium machining as well as assembly and logistics, BÄR is building an additional plant for sheet metal parts and welded assemblies in Šiauliai, Lithuania. It is to become the most efficient plant in the industry. With state-of-the-art machines such as the highly dynamic 7-axis welding robots, which work together synchronously in conjunction with the latest welding technology and record all machine data in real time. But also with decades of production experience, a motivated team and a clear growth strategy. The future can come.
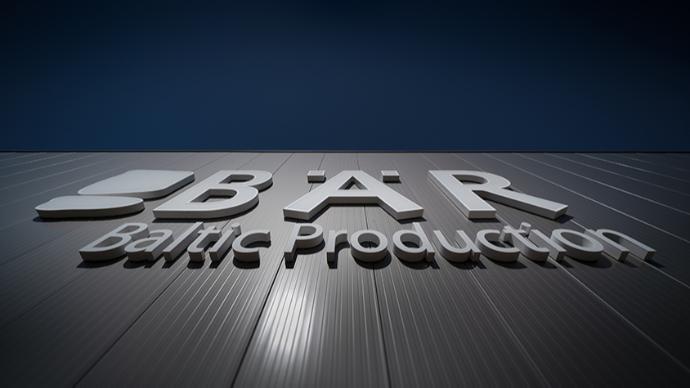
Bär SmartControl CabControl for easy docking at the ramp (2020)
Loading and unloading at the ramp with a tail lift used to require a lot of practice, good nerves and a lot of time. The Bär SmartControl CabControl makes this process much more efficient. This is because it enables operation from the driver's cab. In addition, the hand-held transmitter can also be used as a radio remote control.
Investment in the core competence of aluminium machining (2019)
In 2019, the family-owned company is investing 3.5 million euros in its production site in Heilbronn, Germany. A large part of the investment will go into the core competence of aluminium machining. The new machining centre automatically extracts the required aluminium profile and then positions and machines it using state-of-the-art sensor technology. The welding robot then turns these profiles into BAplan platforms. Two new welding robots are also part of the investment. In addition, the assembly material and spare parts dispatch areas are being expanded and professionalised. Because the BÄRs still have a lot of plans!
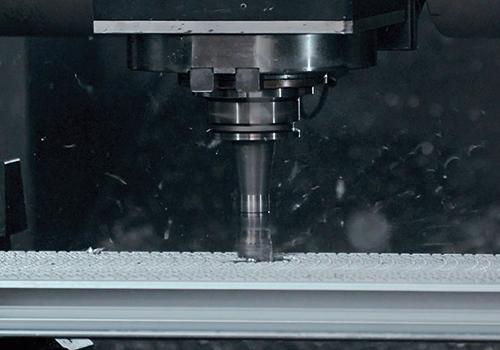
Bär Control EVO (2017)
Innovation by tradition - the tried and tested is retained, potential for improvement is implemented, innovative technology is developed. This promises the highest level of development of the Bär control unit.
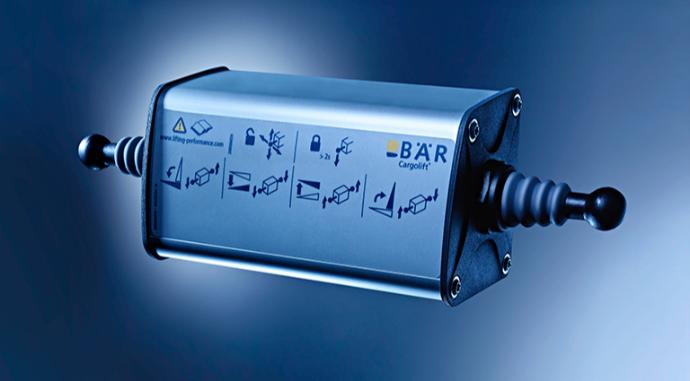
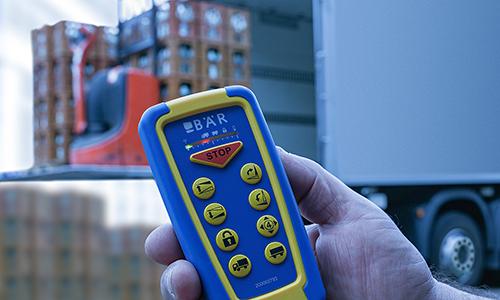
Safe operation by radio - Bär SmartControl remote control (2014)
The Bär SmartControl operating concept gets a practical terminal in 2014: The Bär SmartControl remote control with close-range detection. It raises the operation by radio to a new safety level and allows the operation of both Cargolifts with one hand-held transmitter.
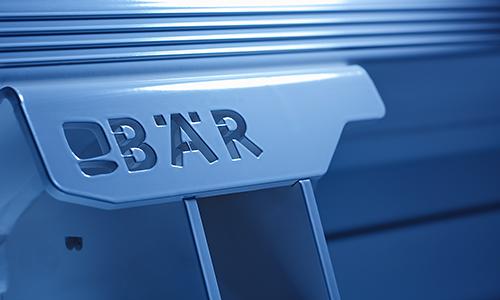
The next generation of the BAplan platform (2014)
In its enhancement, the BAplan aluminium platform changes from 40 mm to 45 mm thick aluminium profiles. This reduces the platform weight by around 18% and at the same time increases stability by 9%. The sheet metal back box is replaced by an aluminium extruded profile, creating a larger advertising space at the back of the platform.

Light and robust at the same time? With high pressure! (2014)
The new BC 1500 S4L is the first Cargolift to receive the new high-pressure technology in 2014. S4L is operated at 310 bar - instead of the standard 220 bar. High-strength steels and the new BAplan45VLL platform system provide further weight savings.
The next generation (2012)
Thanks to the new eBC Controller, service work is now supported by the diagnostic and service software Bär CargoCheck.Bär CargoApp (2012)
The Bär CargoApp accesses the Cargolift via Bluetooth and enables remote control via smartphone "Bär SmartControl" as well as fault diagnosis of electrical faults.Bär CargoWarn (2012)
The overload indicator Bär CargoWarn warns in case of overload during unloading and thus prevents violent damage.To protect the platform corners - RamGuard (2010)
When using the standard platform on the ramp or also when manoeuvring to the rear, the stainless steel cover protects the platform corners.
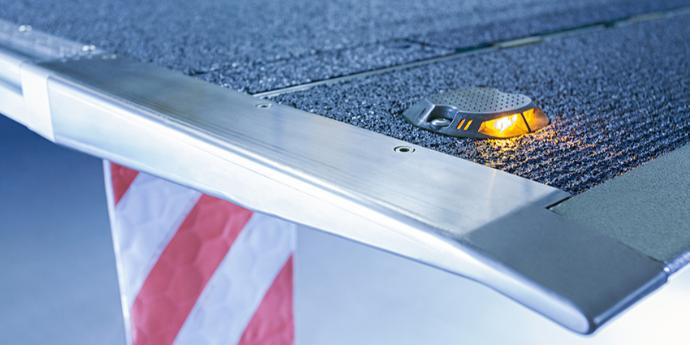
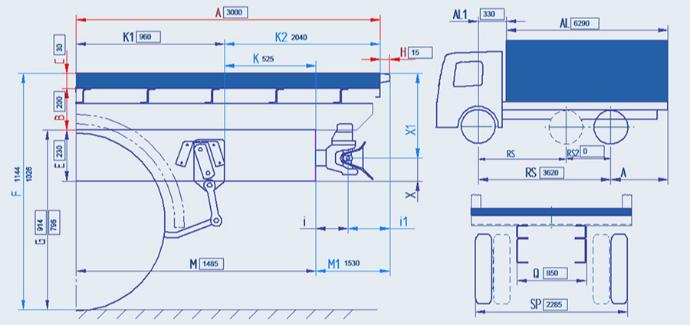
Fitment calculation made easy (2008)
With the digital fitment calculation programme, the installation check at Bär can be carried out online since 2008.
Further expansion of the production area to 9,000 sqm (2007)
The production of aluminium platforms is further expanded. Bär Cargolift sells about 14,500 Cargolifts in one year for the first time.
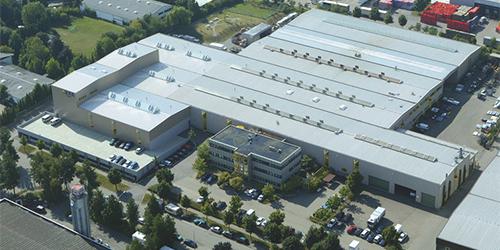
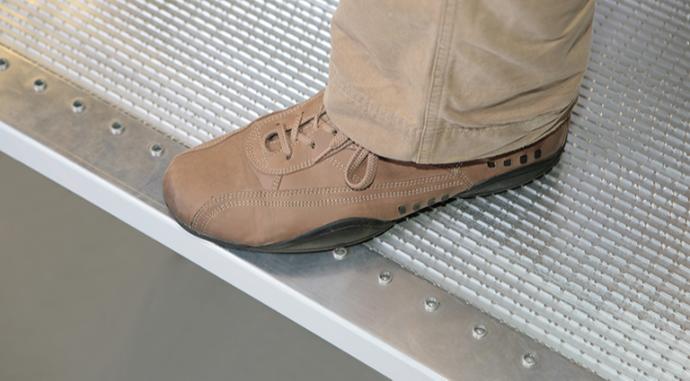
All-aluminium platform concept BAplan with TracGrip (2006)
Bär develops the platform concept BAplan with upright aluminium profiles and the anti-slip platform surface TracGrip - developed and manufactured at the traditional location in Heilbronn, Germany. Thanks to the consistent use of aluminium, BAplan is lightweight construction "Made in Germany". Adapted to load capacity and application, all BAplan platforms have the optimal ratio between stability and weight.
Hall extension at the Heilbronn production site (2004)
The topic of securing the location gains in importance. Bär creates space for its own platform production and enlarges the Cargolift assembly line.
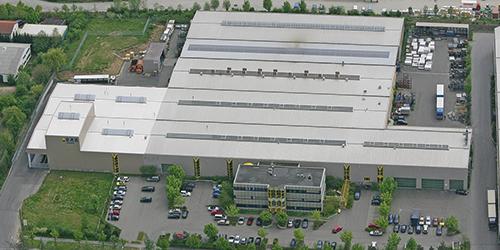
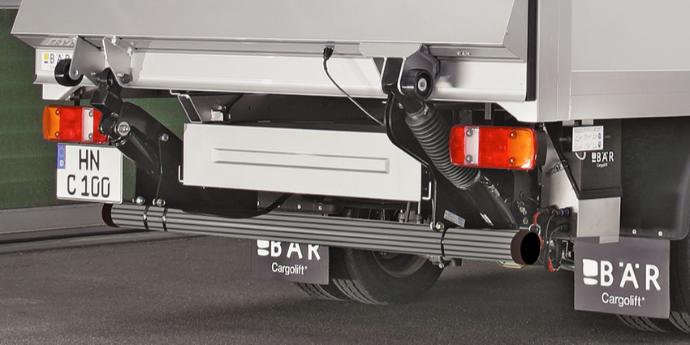
What power does depends on how it is used. The 2=4 technology (2002)
2=4 - the Bär formula for maximum efficiency with low lifting capacities, medium platform heights and standardised vehicle structures. Because it is not the number of cylinders that is decisive. With its 2-cylinder series, Bär presents a new way of power distribution that is even superior to many 4-cylinder models.
Bär presents its Alpha series (1998)
Greater stability and sufficient power reserves for higher platforms, the optimised mechanical joint without critical point, a proprietary sealing system for permanent sealing, even when the platforms are completely closed - even for bodies with nitrogen cooling without doors. These advantages make the "Alpha" series a new, future-proof standard.
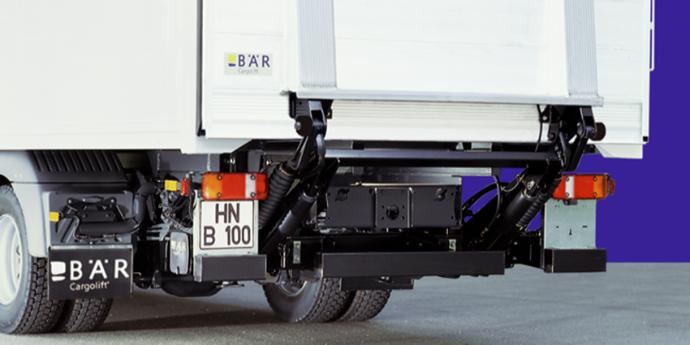
Big. Strong. Bär.
The double-decker lift (1995)
A true milestone for the robustness of Bär Cargolifts. Because the double-deck lift is a lift of superlatives: 3,800 mm platform height - fully closing and insulated, 3,000 kg lifting capacity, 1,650 mm load distance and a load moment of 49.5 kNm! The huge platform holds up to six pallets or ten roller containers. Thanks to the hydraulic ramp support, the large platform can also be driven over with heavy industrial trucks. The operation for lifting and lowering as well as for the hydraulic extension of the ramp support is carried out comfortably and safely via a radio remote control. The lift can not only be loaded and unloaded from the ramp to the lower or upper floor and vice versa, but also to the floor. In the meantime, the double-decker lift is unfortunately a relic of a bygone era.
Launch of Bär Cargolift HydFalt with aluminium guide mechanism (1994)
The principle of the "under-swing lift" in a new dimension: Bär Cargolift HydFalt as the first fully hydraulic folding retractable lift is not only comfortable, but also decisively faster when used frequently. HydFalt, with the world's first aluminium sliding mechanism, is completely pre-assembled and simply bolted to the vehicle frame.
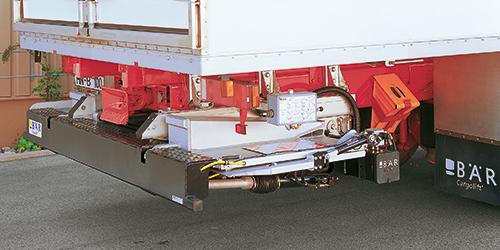
The new aluminium platform with 10% less weight and 30% more stability (1988)
The superstructures are getting higher and higher. With them, the body-closing platforms - and thus also the load moment. In this context BÄR presents its solution: a new platform construction, flat and with aluminium support beam. Above all, the intelligently designed, transversely laid 40 mm profiles ensure lasting roll-over resistance. The design is typical BÄR for many years.
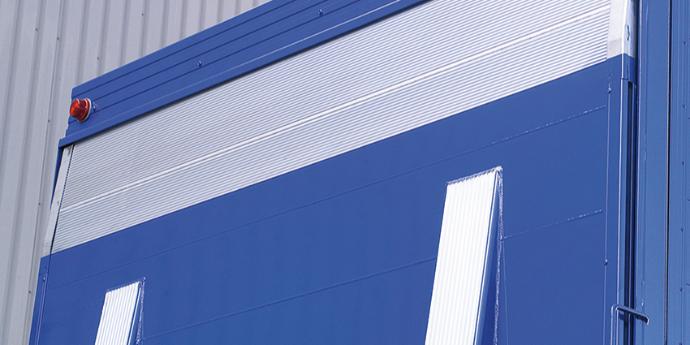
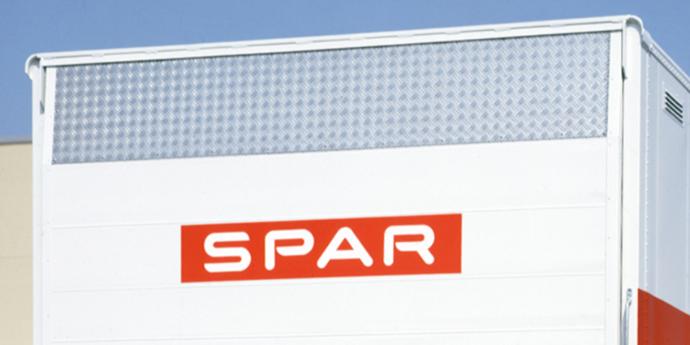
The first fully closing aluminium platform (1985)
When using tail lifts with box bodies, the box flap always has to be operated as well. In addition, there is only room for two roll containers on the small platform. At the IAA 1985, BÄR presents the first fully closing, conical aluminium platform on the BLW 2000-23 with a load moment of 18 kNm and a new, pneumatic trolley stop for four roll containers.
First under-swinging, twice-folded tail lift (1983)
The logistics industry is constantly evolving. This is also the case in 1983: The tail lift interferes with trailer operation or docking at loading gates. The Bär solution can be swivelled under and folded twice! An outstanding innovation that not only fits standard freezer boxes, but also ideally complements the BDF swap systems that were becoming widespread at the time.
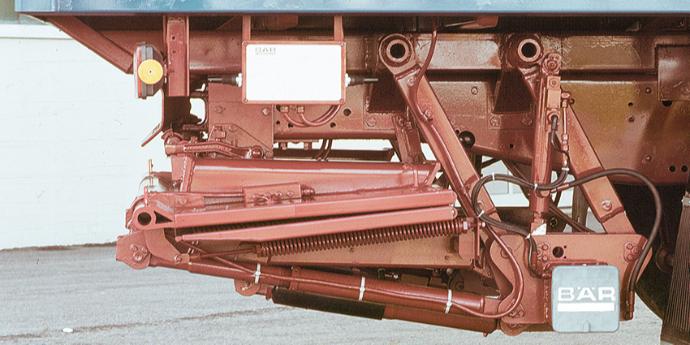
Intuitive operation right from the start (1981)
The ergonomic operating unit with two cross-lever switches, which is new at the time, already uses today's operating logic and, thanks to its robust design, no longer requires a protective box.Safely packed in the support tube (1981)
Because Bär places the entire hydraulic unit including lines and electrics in the square tube right from the start. Safely protected and typically Bär.The mechanical joint - one of the first Bär patents (1981)
Smooth, automatic tilting up and down on the ground - even with full load! The operator sets the platform to the most work-favourable tilt angle when opening it, which is then maintained unchanged throughout all load cycles.To install this Web App in your iPhone/iPad press and then Add to Home Screen.